Ipe Decking Installation
How to Build Your Deck
Building an Ipe Deck:
For many, building a deck with ipe decking is a rewarding experience. Whether you hire a local deck builder, or plan on making it a DIY home improvement project, the end result is the same. When the last board is fastened and the coat of deck oil has dried, you can take comfort knowing that you just created a long-lasting and beautiful addition to your home. So, let’s get started!
Prior to Installation:
Know the difference between air-dried and kiln-dried decking before you buy ipe! Air-dried decking will normally contract. Air-dried ipe is recommended for outdoor applications like decks, benches, siding, and outdoor furniture. Kiln-dried decking will expand due to the moisture content in the air plus all the rain and wet weather that it may come in contact with. Kiln-dried ipe is ideal for indoor applications.
It’s absolutely critical that you account for adequate ground area ventilation in your deck design. Proper air flow will increase your deck’s stability.
Once your order arrives at the job site, you should let your ipe decking acclimate to your climate for a number of days. This is important because you will allow the decking material to settle to your area’s temperature and humidity levels. An appropriate level of moisture content is approximately 12%.
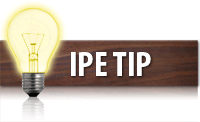
If you’re building a sunroom, you might be confused about whether to use air-dried or kiln-dried ipe. If you’re installing over a subfloor with heating and air conditioning, use kiln-dried. If you’re installing over joists with open air and no climate control, use air-dried.
Cutting and Drilling:
Ipe is an extremely dense wood and is difficult to work with. Inadequate equipment will quickly loose its edge. A reduced cutting angle is required for molding or planing. Pre-drilling for screws is HIGHLY RECOMMENDED. We don’t recommend using nails, since nails can pop out over time. Nails are also tend to cause splits. Here are the tools we recommend:
- Carbide-tipped saw blades
- Protective eyeware
- Brad point drill bits
- Forstner bits
- Torx screws
- Stainless steel trim-head screws
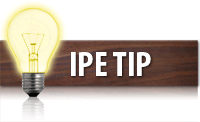
Looking for a deck builder? Ask if they have much experience workign with ipe and what tools they use. Also ask to see their portfolio of ipe decks. If you can get permission, it also helps to see some of their decks in person.
End Sealing:
End sealing is highly recommended with fresh cuts of ipe. Using an end-grain sealant within 24hrs of cutting the material is standard. When you buy ipe decking from our company, you need to know that your shipment will be sealed with a clear wax to prevent end checking. Applying endgrain sealer is easy. All you need is a cheap paintbrush and the sealant will dry on clear.
Fastening Methods:
By far, the topic that brings the most discussion amongst deck builders is “What is the best deck fastening method?” There are three major ones that are worth mentioning. Using nails to install an ipe deck is not recommended and, quite frankly, a waste of time. Besides, when using nails to build a deck, nail pop ups will be an issue over time. Not only is this a liability issue, but it can lead to an unstable decking surface.
Hidden Fastener Method: There are many brands of hidden deck fasteners. While the final choice is up to you, the fastening method we recommend works best with the Ipe Clip® brand of deck fasteners. Their brand of deck fastener firmly holds ipe deck boards in place. They also provide maximum holding power to the joist. Unlike deck fastening systems that requires screws to be installed vertically, the Ipe Clip® deck fastening system requires deck screws to be installed at a 45° angle. It’s been scientifically proven that installing hidden deck fasteners at a 45° angle will produce a much more stable, solid deck.
Screw and Plug Method: If you are committed to installing ipe deck boards with screws only, here are our recommendations:
- Countersink a 3/8” hole into the face of the deck board
- Pre-drill a pilot hole straight through the board using a 1/8’ drill bit
- Use 305 or 316 grade stainless steel deck screws
- Screw the ipe deck boards so they hold firm to the joist
- Use wood plugs to fill the holes. 3/8” deck plugs are available in a number of hardwood varieties
- Use a waterproof glue (e.g., Epoxy or Gorilla™ brand of wood glue) and glue the wood plug into the hole
- Any exposed portion of the wood plug can either be sawed or chiseled and then sanded until smooth
Finish Screw Method: Follow steps #2, #3, and #4 from above. Use stainless steel #8 trim head screws. These screws have heads that are smaller than normal deck screws because they are less noticeable. Screw straight through the face of the decking. We recommend screwing two screws per joist.
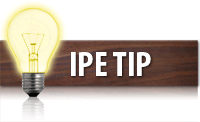
Deck builders prefer using torx screws for hardwood decking. These screws resist striping much more than normal decking screws.
Nominal Dimension | Joist Spacing |
1x4 | 16" |
1x6 | 16" |
5/4x4 | 24" |
5/4x6 | 24" |
2x6 | 32" |
Joist Spacing:
This span chart offers conventional joist spacing sizes and meant to have nearly zero deflection under standard loads. Please contact your local permit and building code department for proper joist spacing requirements. The joist spacing shown is also valid if the decking is laid in a diagonal pattern to the joist. The spans shown are typically used even with heavy loads such as hot tubs.
Gap Spacing:
A 1/16” gap between ipe deck boards is recommended. This will allow the ipe decking to expand and contract without abutment. 1/16” gap spacing is also adequate for air circulation and water drainage.
The average contraction of a 4” wide ipe deck board is approximately 1/16”. With a 6” wide deck board contraction will be approximately 1/8”.
Finishing:
KILN-DRIED / INTERIOR APPLICATIONS: Areas that are exposed to heat or air-conditioning will need to use interior kiln-dried ipe. You can acquire this product in prefinished or unfinished. If you decide on an unfinished product then it should be finished with a polyurethane blend finishing solution.
AIR-DRIED / EXTERIOR APPLICATIONS: Deck oil can be applied to air-dried decking applications that are exposed to the elements (decks, porches, patios, etc). We suggest finishing the decking once it has been installed if they are planning to do only a top coat. You can also apply the finish to all 4 sides of the decking. Decks that have very little ventilation will need to apply the finish to all four sides of the decking prior to installation. Finishing all four sides of the deck boards will ensure equal moisture content on all sides of the boards. It will also help to stabilize the material after installation.
TYPES OF DECK OILS: By now, you already know that ipe is a naturally dense wood that has alkaline characteristics. As a result, most finishes that are made of oil and water don’t dry properly and create a blotchy looking surface. Before you apply any deck oil, test the finishing solution on a few deck boards and see how they dry. If the finish is uniform and clean, you can proceed with confidence.
Decking oils that work well with ipe decking include Ipe Oil™, Messmers UV Plus, CWF Flood Finish, and Sitkens Deck Finish. Upon application, your ipe deck will darken slightly. However, these finishes are meant NOT to stain the decking. They protect the wood and will prevent your deck from fading and the sun’s U.V rays. Around 6-8 months later, you can apply another coat. Apply a fresh coat either once a year for the first two years and then every other year after that. The material itself will maintain its color for its entirety as long as the oil finish is applied.
Gluing:
For whatever reason, if you need to glue a couple of deck boards, we recommend polyurethane based glues or epoxy glues. Epoxy glue can offer a durable and waterproof bond plus, it can be dyed to match the color of your decking. Wiping your glue edge with acetone before gluing will help with adhesion. This takes the natural oils out of that surface for a short period of time so the glues can penetrate and create a better bond.
Ready to Build?
If you have questions about the installation process, or if you’re ready to order, fill out our online quote form or give us a call at 1-877-232-3915.